Home > Filter elements > Vacuum filter belt
Filter belts for vacuum belt filters
K2TEC is a recognized manufacturer of filter belts for vacuum belt filters. Thanks to more than 30 years of experience, a specialist chooses the most suitable type of fabric for each application. The filter cloth will be selected to optimize the filter efficiency, the dryness of the cake or the sludge.
K2TEC, thanks to its experience in the field, is able to respond in an optimized way to the technical elements around the vacuum belt filter. For this purpose K2TEC has a knowledge of industrial filter fabrics and will select the best filter cloth, which will be a compromise between efficiency, clear filtrate and cake or sludge dewatering.
But the vacuum filter belt is not just a filter cloth. K2TEC has also worked on filter belt junctions, developing fast, simple, robust and removable solutions. The ultimate area of research has been to work on side reinforcements with or without technical coating in order to protect the filter belt as well as possible from the mechanical stress of the belt filter.
Highlights of the K2TEC vacuum filter belts
complete range of filter cloths
of more than 30 years in the filter belts manufacturing
for the closure system of filter belts
double layer cloths available in widths over 4000 mm wide
How does vacuum belt filter work?
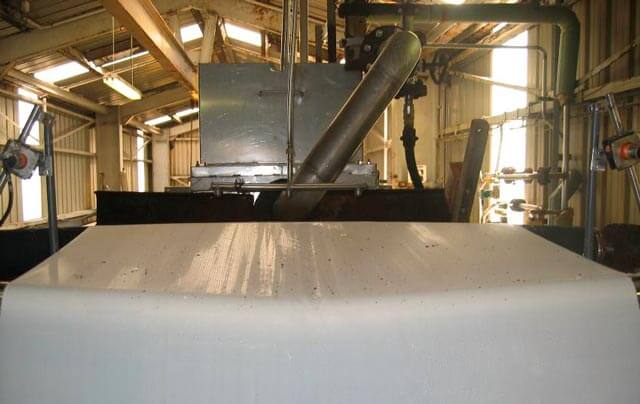
The vacuum belt filter allows a continuous solid/liquid separation. The product to be filtered is deposited on a filter belt which is driven in rotation.
For the vacuum belt filter:
Under the filter belt, vacuum boxes create a vacuum in order to increase the filtration speed, as well as the dryness of the filter cake.
For the pressure belt filter:
The product arrives through a closed and tight enclosure on the belt. The result is more or less the same as for the vacuum filter but it is possible to increase the pressure and therefore the dryness of the filter cake.
For the belt filter press:
The sludge is sandwiched between two filter belts. The space between the two filter belts decreases evenly and presses the cake to dewater it.
For the gravity belt filter:
No mechanical action is made, neither by pressure nor by depression, it is gravity that creates the hydrostatic pressure that leads to the filtration.
At the end of the filter belt, whatever the system, the cake is discharged by means of a scraper or a brush or by a simple change of angle.
Filter cloths for vacuum filter belts
For the manufacture of vacuum filter belts, there are 4 main types of filter cloth.
The choice is mainly guided by the filtration rating required, but also by the chemical environment and especially the mechanical resistance.
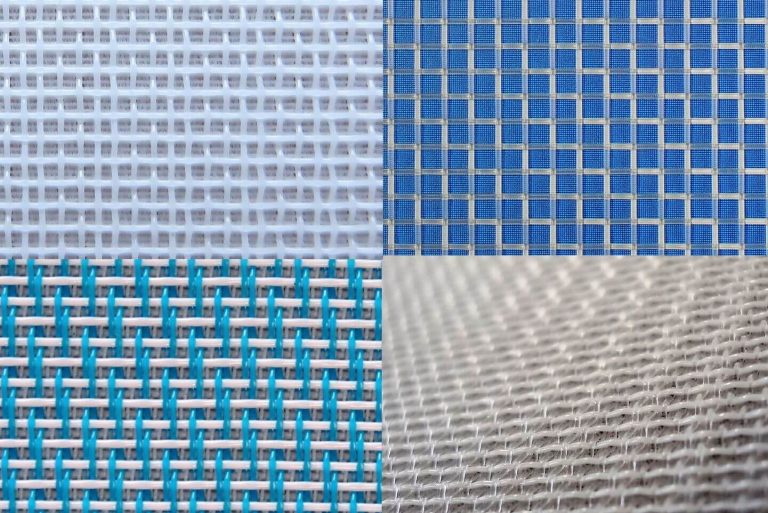
Monofilament filter cloths are made from extruded monofilament synthetic fibres, allowing complex weaves for precise filtration ratings.
These industrial filter cloths have the advantage of being easily regenerated by washing or blowing and have high non-stick properties.
Filters using monofilament cloths are essentially high efficiency filters of all types, with automatic or manual deaeration.
Multifilament cloths are made from synthetic fibres that allow complex weavings that are either light and inexpensive or heavier and complex weavings.
Multifilament cloths can be used either in process filtration or in filtration of coarse rejects. This filter cloth has the enormous advantage of being stable but above all it has a great capacity to filter very fine products such as pharmaceuticals or pigments.
Monofilament / multifilament filter cloth is widely used on belt filters, mainly for mechanical strength but also for the ease of filter cake discharge.
It combines the best of the two technologies: multifilament with good mechanical resistance in the weft and warp direction and monofilament with the ease of filter cake discharge.
The double weave technology comes from the idea of associating a complex weave with a very fine filtration rating with a support fabric with high mechanical resistance. This type of fabric has the advantage of being highly mechanically stable in both longitudinal and transverse directions.
The double weave enables a constant yield and permeability to be obtained over time. Thanks to the monofilament structure, the filter cake is easy to discharge and of very good quality. For this type of product K2TEC has a range of filter cloths based on Polypropylene, Polyester or PVDF with widths up to 4300 mm.
Applications of filter belts for vacuum belt filters
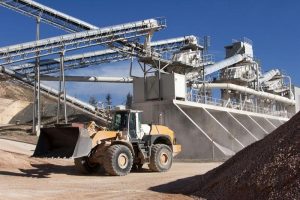
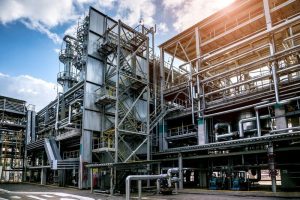
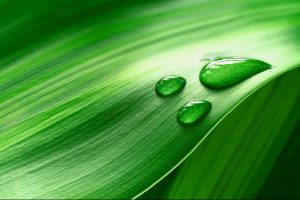
Do you have a filtration inquiry ?
Filter cloth materials for vacuum filters
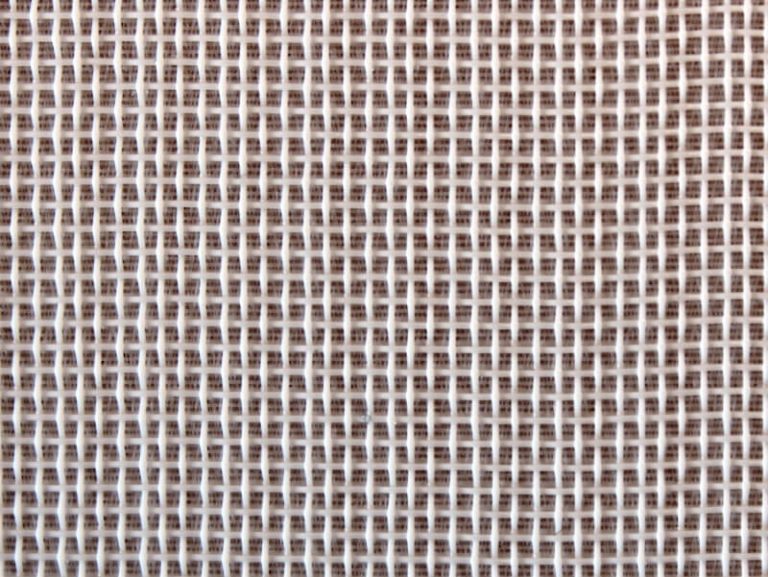
Vacuum belt filter cloths can be made of polypropylene (PP), polyester (PES), polyamide (PA) as well as more specific materials such as PVDF or PTFE (commonly called Teflon).
The material of a vacuum filter belt cloth must reflect not only the chemical environment, but also the qualities required by the process and the product. Some materials are more or less hydrophobic or hydrophilic, some have more or less non-stick qualities etc… It is therefore necessary to integrate these elements in the final choice of the material of a belt filter cloth.
Filtration rating of a vacuum filter belt
K2TEC filter cloths are measured according to the Bubble Point test. This test is used to measure a filtration rating under pressure. The cloths can have filtration ratings ranging from 1 micron to 2000 microns; a certain dispersion and more or less narrow tolerances can be observed and must be taken into account.
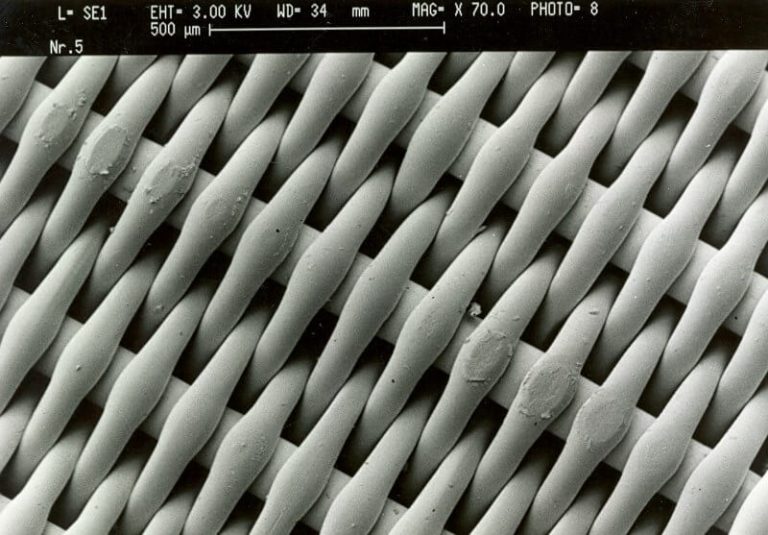
Filter belts closure systems for vacuum belt filters
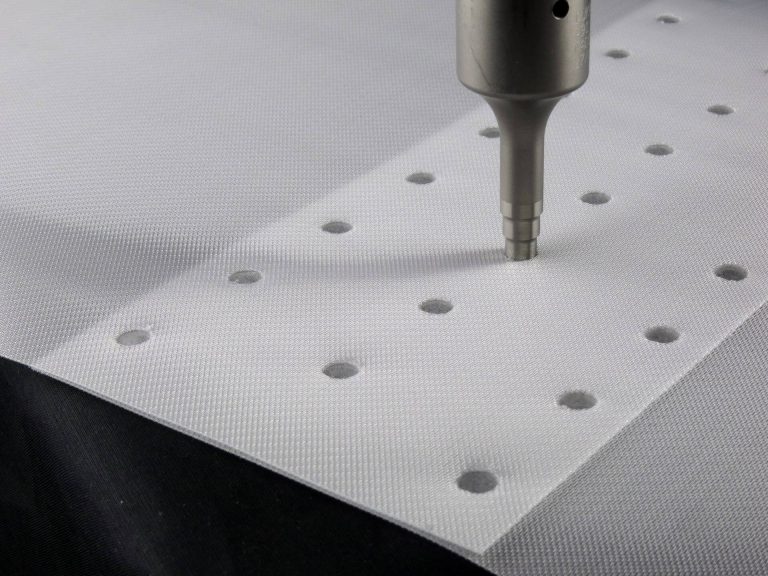
The junction and closing of a filter belt is often a delicate operation, that is why, thanks to its experience, K2TEC has developed different techniques depending on the manufacturing process and the size of the vacuum belt filter. There are currently three solutions to close filter belts:
– on-site ultrasonic welding
– synthetic closures
– stainless steel closures
Edges reinforcement
Vacuum filter belts edges can be reinforced in 4 ways:
Hot cut edges: most belts are simply hot cut. This cutting is more effective than a simple cold cut to avoid fraying.
Coated edges: the purpose of coating is to avoid lateral fraying over the long term and to help guide the belt on certain types of filters (such as Pannevis or BHS).
Stitched edges: the edges of the belt can be reinforced with a piece of fabric sewn on one side or both sides.
Stitched edges with coating: the edges can also be reinforced with a piece of fabric sewn and then coated. This technique facilitates the passing through the vacuum belt filter and provides the longest service life.
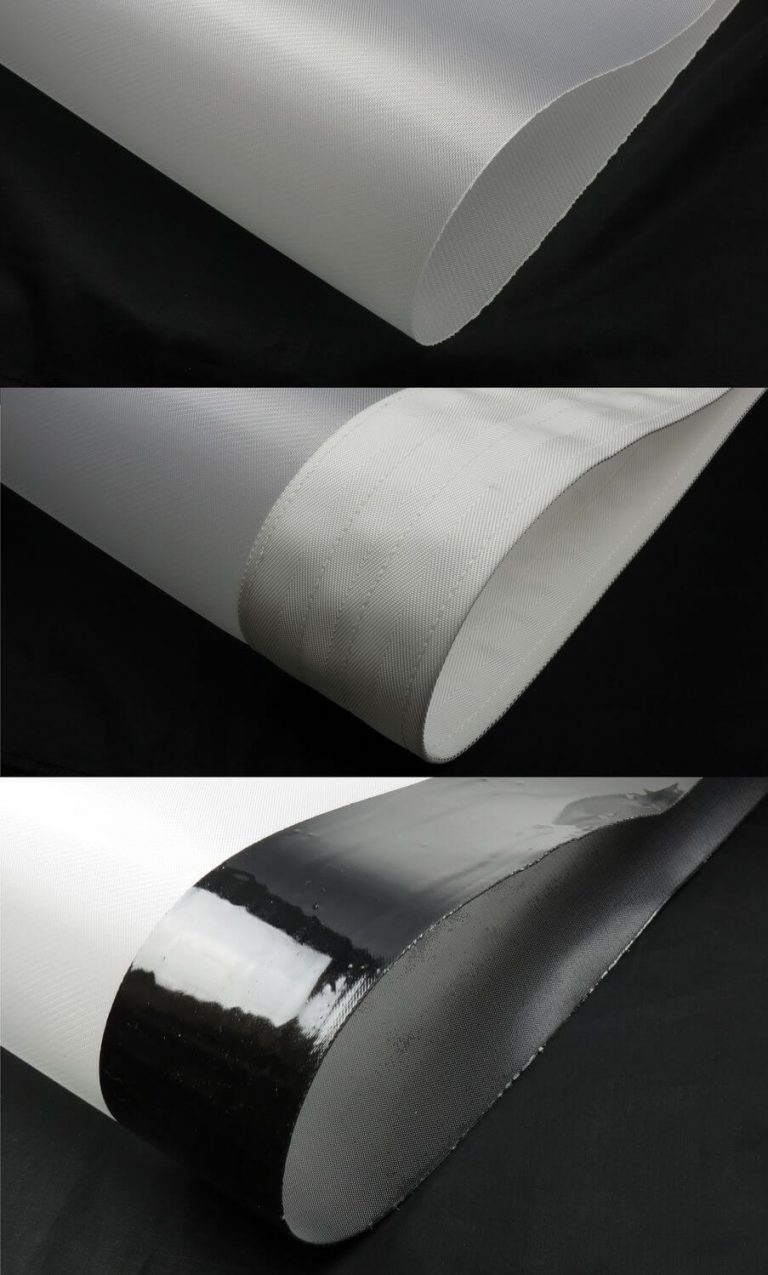
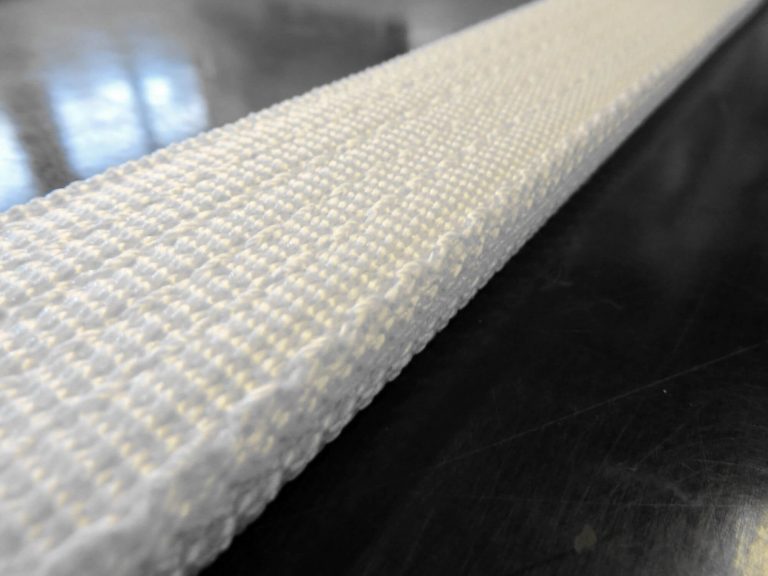
Regularly in contact with vacuum belt filter users, K2TEC also manufactures wear belts for vacuum boxes.
In vacuum filters, these wear belts take up the vacuum load and provide a seal between the fixed part (vacuum box sliding strips) and the rotating part (filter belt).
As a replacement for the rubber belts for Philippe RPA or Pannevis Filter, K2TEC manufactures polypropylene belts, which are very mechanically and chemically stable. The belts are available in several sections, the most common being 38x10mm, 28x6mm and 50x5mm. They are also much more inert than the original rubber belts and are compatible with most chemical environments.
These other filter may interest you :
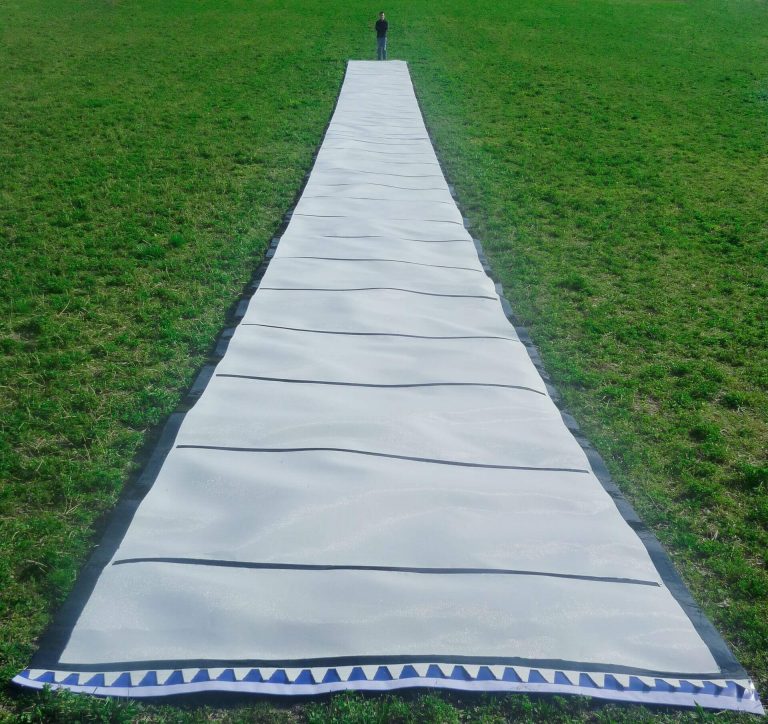
Coolant filter belts
Manufacturer of industrial filter belts for coolants, oils and emulsions in the mechanical industry. 30 years of experience in filtration.
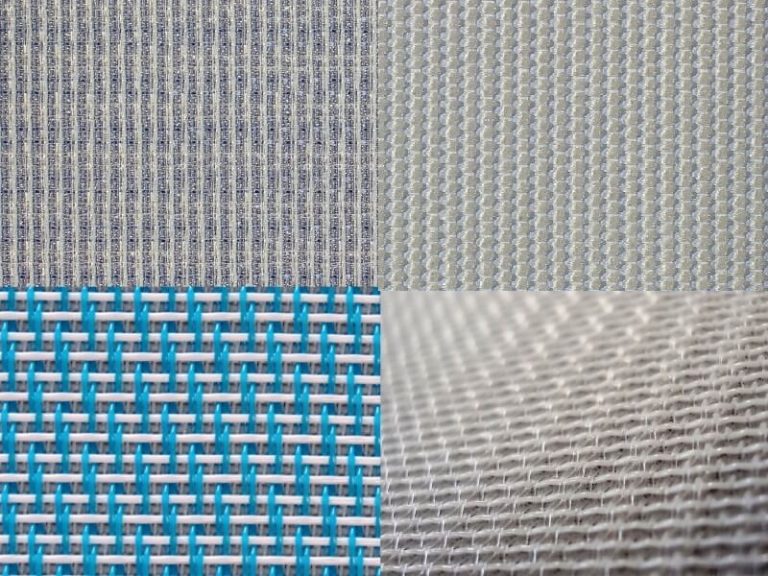
Filter cloths
Nylon, polyester, polypropylene, PTFE… filter cloth for industrial filtration, and for the manufacture of custom-made filter elements.
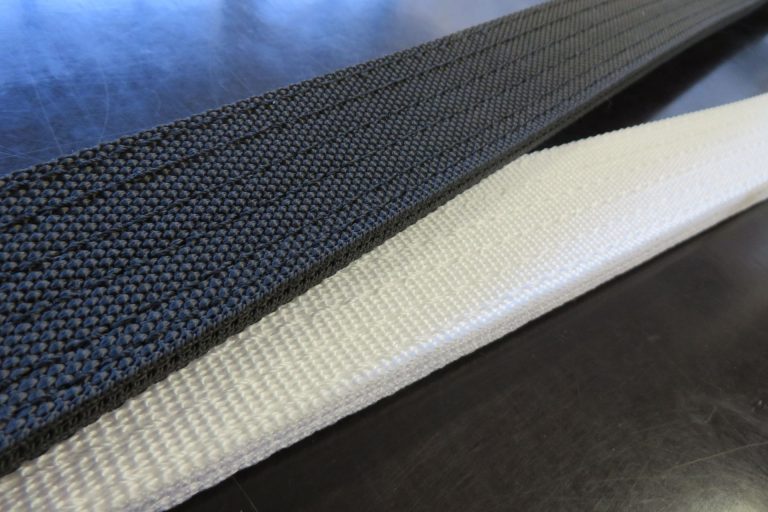
Wear belts for vacuum boxes
Product application K2 Tec Wear belts for belt filter vacuum boxes The vacuum belt filters have been used for many years in different industrial process