Home > Filter elements > Custom filter elements

Design and manufacture of custom filter elements and filter components
For more than 30 years, K2TEC has been a leading provider of industrial filtration solutions, including the design and manufacture of custom filter elements.
Our extensive experience in the field allows us to provide tailored solutions to satisfy the most diverse applications. We analyze the need, choose the right filter fabric, and define the implementation to maximize customer satisfaction.
K2TEC can manufacture from simple die-cut filter pads to complex laser-cut and ultrasonically welded parts on a molded plastic bracket.
Our high-precision fabrics are used to produce everything from simple parts such as tapes, discs, flat shapes or more complex applications such as filter screens, filter cartridges, pleated cartridges, tubular filter elements, filter candles, and more. K2TEC develops and manufactures filter elements on request according to your specifications.
The strengths of K2TEC filter elements
over 35 years
we analyze your needs and craft a relevant quotation
filter mesh, filter cloth, non-wovens, precision synthetic filter fabrics, etc.
laser cutting, sewing, ultrasonic and high-frequency welding, gluing, molding; and more.
The different types of custom-made filter elements
It is difficult to draw up an exhaustive list of custom-made filter elements. The following short list gives a few examples, but often the only limit in making a custom filter element is… your need.
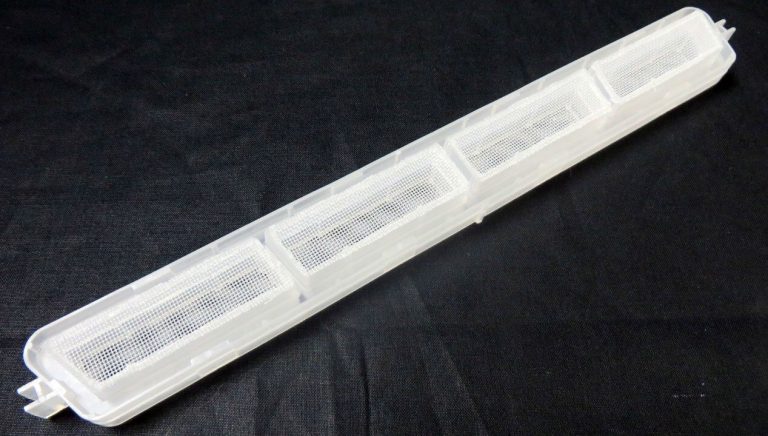
Medical filter
Medical filters are used in breathing apparatus, blood analysis devices, hand sanitizer devices, etc. These custom-made filter elements meet strict cleanliness standards and are manufactured from specific CE-approved filter fabrics. Medical filters can be flat cut shapes or ultrasonic welded filters on brackets as well as molded filters for large quantities.
Molded filter
The molded filter is used for a wide range of applications. Molding is a commonly used operation, especially for the production of filter elements in large quantities or with high precision.
Commonly used materials are polypropylene, polyamide, and polyethylene.
The molded shapes can be simple flat filters or strainers, but they can also have complex shapes optimized for filtration surfaces or for integration into machinery.
Simple filter elements: ribbons, discs, custom shapes
In many basic cases, the filter element is a simple filter fabric, which can be laser cut, hot cut, or die cut on a press. These filter elements can be a few millimetres to several meters long and all shapes are possible. These parts are used as they are or sent to other manufacturing stages (molding, ultrasonic welding, etc.).
Tubular filter
Under simple aspects, the tubular filter can be very complex in its manufacture. It can be woven into a seamless tube or ultrasonically welded from two tapes to obtain a tubular shape. The tubular filter is used in the manufacture of strainers. The tubular filters are available in rolls or cut to length.
Filter strainers
The filter strainer is often compared to a filter tube with a rigid plastic or metal frame. The strainer is usually equipped with end caps to fix it in place. The assembly of this type of product is generally done either by molding, HF welding or ultrasonic welding.
Special custom-made filters
Requests for custom-made filters are diverse: filters for household appliances, for automotive, for loudspeakers, for blood analysis… These filters are cut and then generally assembled on a support provided by the customer. K2TEC is equipped to manufacture small and large series and sets up the necessary inspection methods.
Automotive filters
The number of filters on a vehicle is important. Air filtration: cabin filter, air conditioning filter… Liquid filtration: fuel filter, water filter… All these filters are special and manufactured to industrial specifications.
Do you have a filtration inquiry ?
Steps in the making of a custom-made filter element
K2TEC can take action at any stage of the custom filter element design process, either :
– In consulting: which is the right filter media for a bag, a cartridge, a strainer, a static part?
– In study: how to implement the filter fabric in a simple and economical way. Is it necessary to stitch, weld or inject?
– In production: prototyping and then mass production.
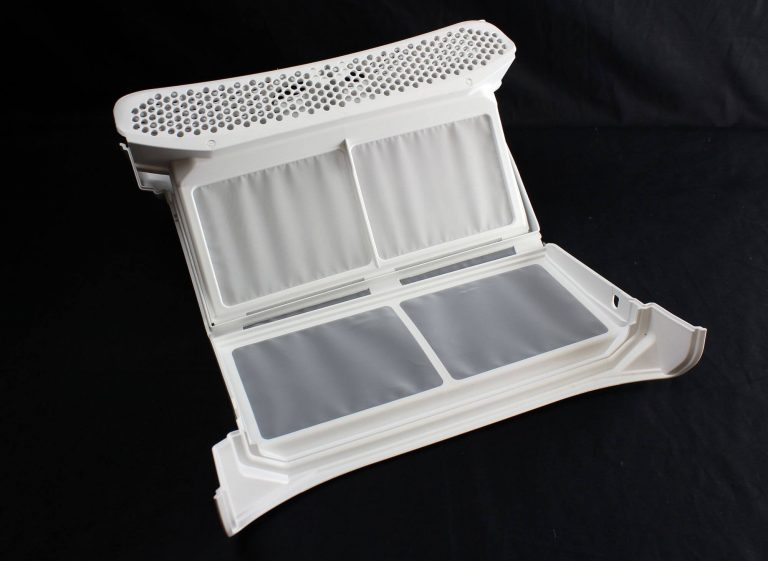
You know the technical environment of your process. You are looking for a filtration function but where do you start? Before designing tools, before manufacturing, machining, injecting, molding your filter… contact us.
Do you want to go further and need technical support? With a K2TEC filtration expert, you will continue the reflection after the first analysis step.
Are we talking about a few custom-made prototype filters or thousands of parts?
For small series of filter elements, K2TEC is able to design, dimension and produce a suitable support.
For medium series, K2TEC’s design office will work with you in collaboration on injected or machined support elements.
For a thousands or even millions of parts we will consider molding, in collaboration with specialists in order to avoid the classic errors of this type of operation as the set-up costs and molds are expensive.
At each step of the realization of your custom-made filter element, K2TEC can act either as a consultant, a design office or a manufacturer.
The filter fabric is the central part of the custom-made filter element. It will be carefully selected to optimize the filtration quality:
– Precision filter fabrics
– Non woven filters
– Filter cloths in monofilament, multifilament, or mono / multi
– Felts from 1 to 200 microns or high efficiency filtration media.
– Available materials: polypropylene (PP), polyester (PES), nylon (PA), PVDF, polyethylene (PE), Teflon (PTFE), viscose…
Are you lost? We are here to help you.
Discover our range of filter fabrics (jump) for a first approach.
An important step in the custom-made filter approach is the price. The advantage of K2TEC is total freedom in the choice of fabric and the control of the process.
There is no need to pay for a molding setup for a hundred pieces. On the other hand, considering an assembly by stitching on series of thousands of complex parts is an economic miscalculation. The specifications, the knowledge of the process and the techniques allow to save on the price of the product.
After validating the specifications, design and pricing aspects, comes the time of production and quality control. K2TEC is responsible for the production of customised cutting and assembly tools. The functional dimensions and mechanical resistance must be checked. For complex parts requiring a thorough and/or unitary quality control, specific tooling may be necessary.
Production means for custom-made filter elements
K2TEC sets up the manufacturing means suited to the type of parts to be manufactured as well as the quantities. From manual solutions for simple parts in prototyping to automated solutions for large series, everything is possible.
Filter cut to measure
You are a user, injector, molder and you want simple parts cut flat or in ribbon form? We carry out the operations in cold cutting, press cutting, hot cutting (illustrated in photo), laser cutting. Simple, special shapes, small or large dimensions, everything is possible.
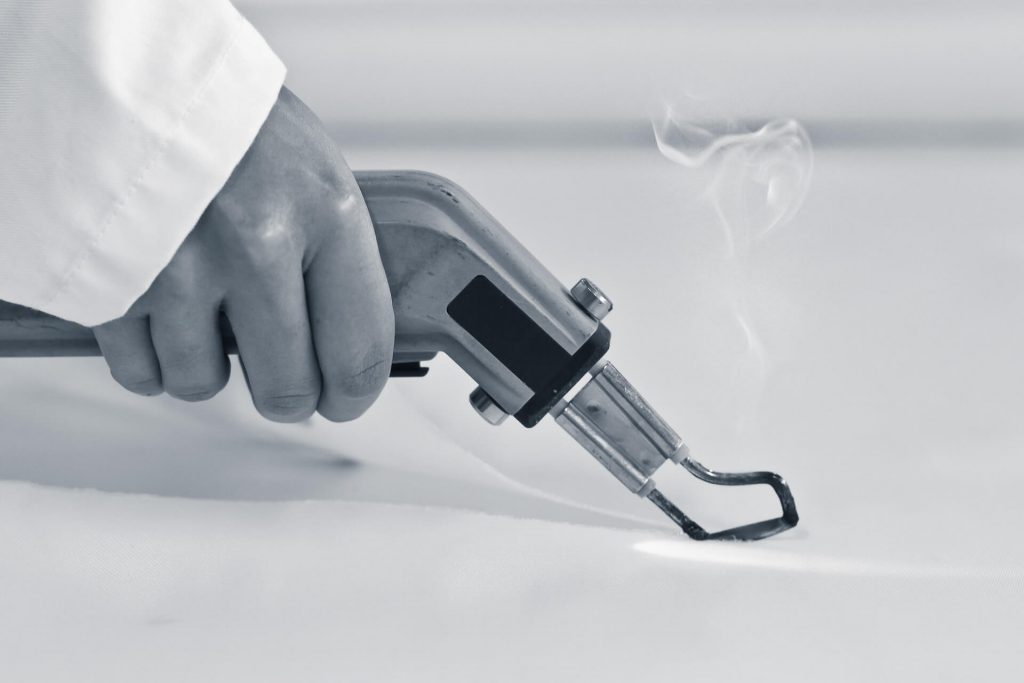
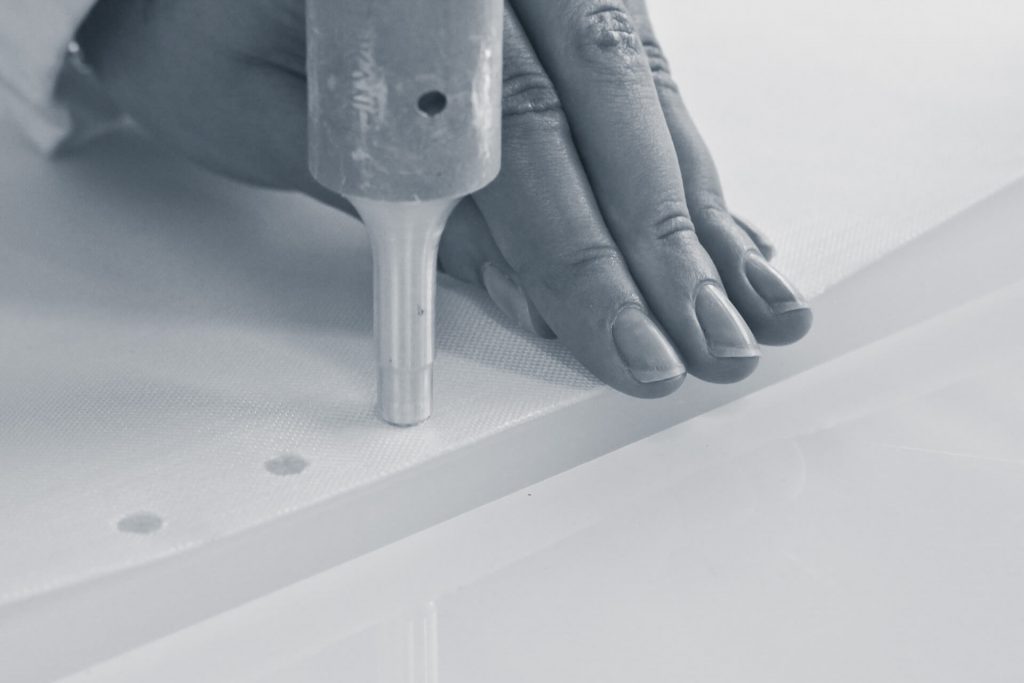
Filter elements assembled by ultrasonic welding
Ultrasonic welding for custom-made filters is a proven technique. The filter is welded using an ultrasonic gun or press. A sonotrode welds the filter to itself or to a plastic support which can have all kinds of shapes.
Molded filters
The molding of filters is the most used technique for large quantity parts, this technique is nowadays perfectly mastered but it hides many tricks. There are few molders who have experience with synthetic filters and are able to use them in good conditions. The molding technique requires special tools and above all a great deal of know-how.
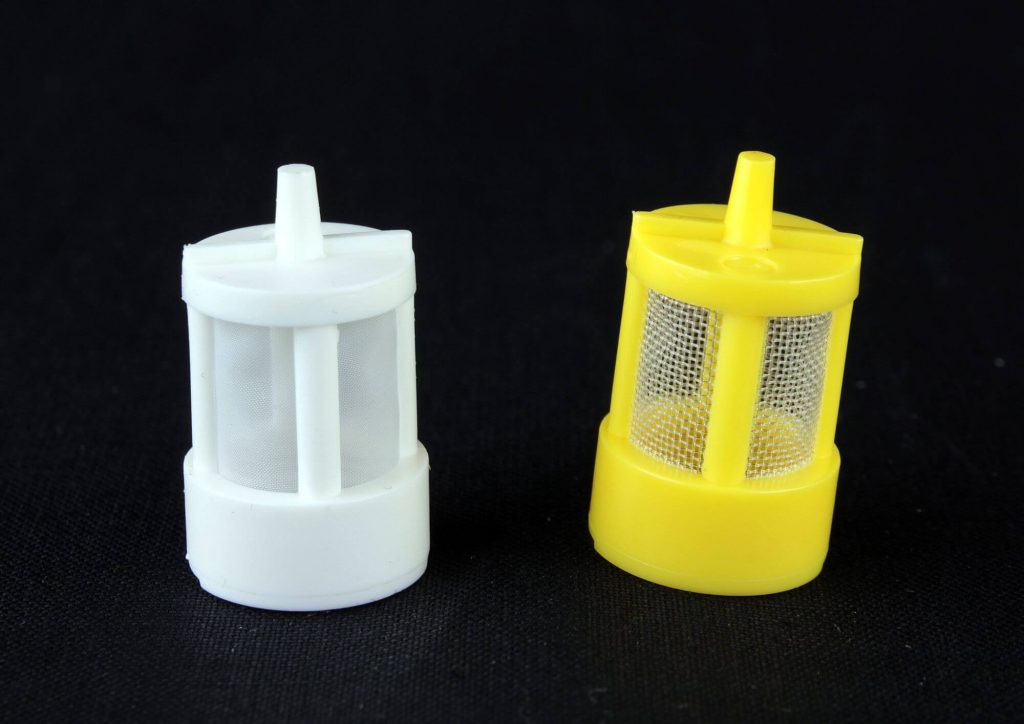
Fields of application of custom-made filter elements
Tailor-made filter elements can be found in a large number of industries:
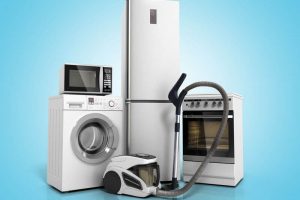
Appliance filters
Dishwasher, dryer, vacuum cleaner, hair dryer...
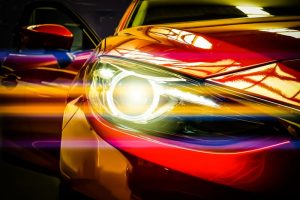
Automotive filters
Injectors, fuel filter, oil filter, exhaust filter, Adblue filter, cabin filter...
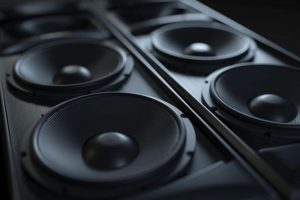
Acoustic filters
Smartphone, headphones, speakers...
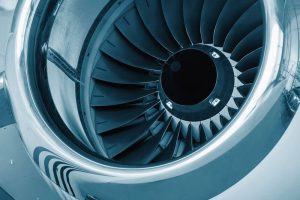
Aeronautical filters
Hydraulic and pneumatic filters, fuel filters, acoustic filters
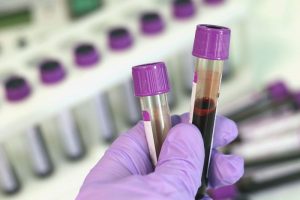
Case study : blood filter
Design and manufacture of blood analysis filters
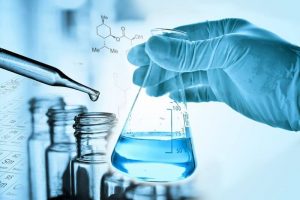
Medical filter
Blood analysis filters, infusion filters, perfusion filters...
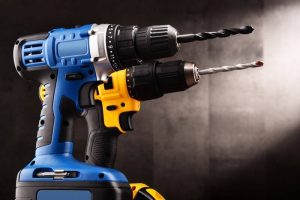
Powertools filters
Protective strainer, flat filter to prevent projections ...
These K2TEC filters may interest you
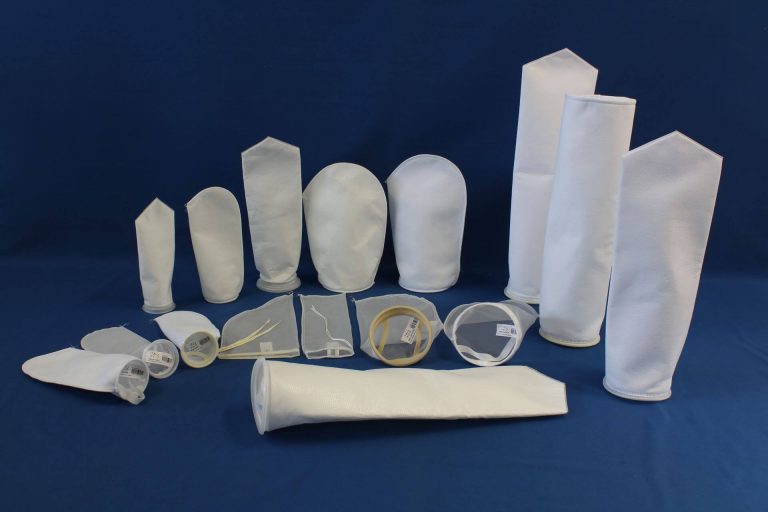
Filter bags
K2TEC manufactures filter bags for the filtration of liquids : complete range of filter bags in polypropylene felts, nylon monofilament, special fabrics…
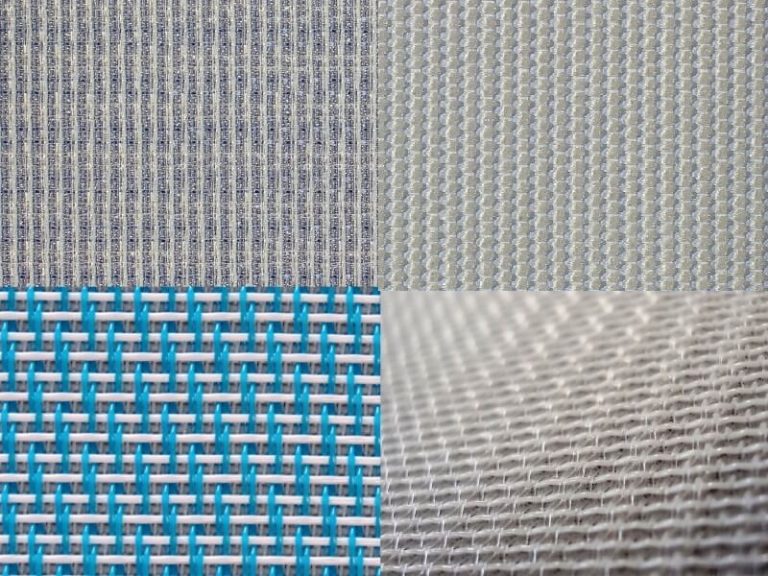
Filter cloths
Nylon, polyester, polypropylene, PTFE… filter cloth for industrial filtration, and for the manufacture of custom-made filter elements.
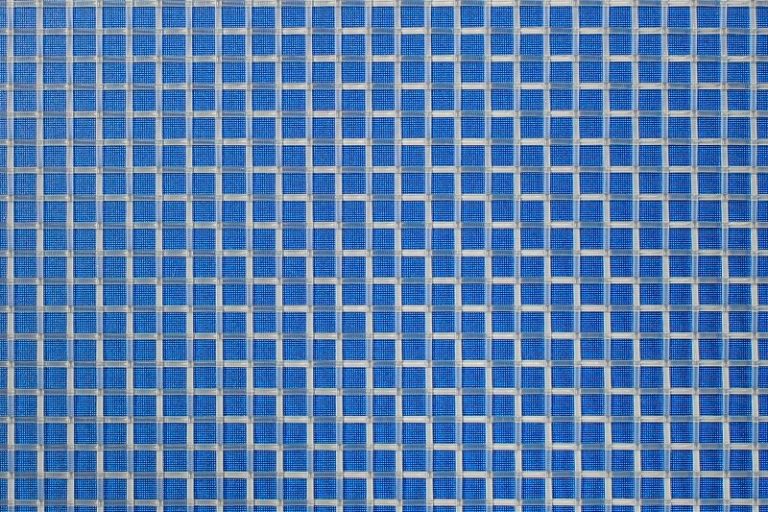
Precision filter fabrics
Precision woven filter fabrics and mesh filter fabrics. An overview of our range of syntethic fabrics for appliance and industrial filters.